Since it was published by the Underwriters Laboratories in 2020, solar racking producers have been putting their structures through a gamut of testing to be compliant with UL 3741: Standard for Safety for Photovoltaic Hazard Control, one of the routes for making rooftop solar projects meet fire safety requirements.
The first few companies to achieve it primarily worked in the flat-roof, commercial solar market, but in the last year, several residential racking manufacturers have achieved UL 3741 compliance.
“Change takes time,” said John de Papp, senior VP of product management and marketing at PanelClaw. “There are a lot of AHJs that still today are just getting up to speed on 3741 and a year ago, they would have said, ‘What is this standard?’”
So, what is UL 3741?
The National Electrical Code dictates industry standards like rapid shutdown requirements, a safety measure for ceasing electrical activity within solar arrays to reduce electrical shock risk. There are three methods for meeting rapid shutdown requirements on solar projects.
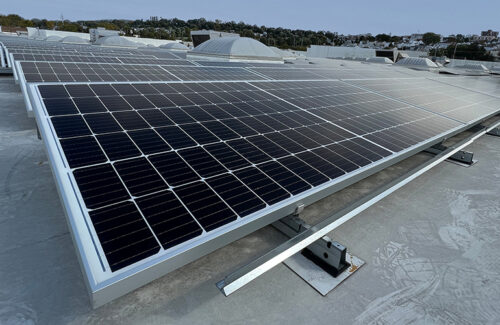
PanelClaw’s clawFR flat roof solar racking is UL 3741 compliant. The company was early to adopt these safety measures for its racking.
The first is using a system that doesn’t require grounding, like building-integrated photovoltaics, because there are no metals present in them. The second is installing a rapid shutdown device on an array. The third is UL 3741, and this standard tests the safety of an entire system instead of just individual components.
“We’re going back to how we built projects before all the module-level power electronics (MLPE) came on the scene, which works great,” said Elie Rothschild, CEO of Sollega.
Certifying that a rooftop solar array is UL 3741-compliant hinges on how the system’s racking and electrical components interact.
First, the array must be capable of rapid shutdown. Cutting power to projects with MLPE on every panel requires turning off every single MLPE. UL 3741 instead recommends using string inverters capable of turning off the entire array from a single location. Using a string inverter over MLPE might mean sacrificing power optimization and monitoring for individual panels, however, optimizing power through MLPE is better suited for roofs with potential shading, and that happens more often on smaller residential roofs than taller commercial buildings.
“Many of [our commercial customers] are not sold on this idea that using MLPEs and having module-level rapid shutdown is inherently safer,” de Papp said. “In fact, a lot of them conclude the opposite is the case, because you’re adding many, many more active devices to the system and you have a lot more interconnects.”
The second consideration for UL 3741 is wire management. Array wiring must be secured using UL-rated equipment, and wires must not be exposed to the elements or resting on any metal surface. Certain manufacturers have designed their racking with channels to conceal wires and provide space for cable runs, and if it’s necessary to run wire between module bays, it must be covered in protective conduit.
“They have all these layers of protection that you have to meet to separate conductors from the actual metal,” said Nicolas Martinez, senior product manager at Unirac. “You have to protect the wire when you’re going from row to row, and make sure that you’re not going over a sharp corner or anything like that. That has to be fully supported along the side of the modules.”
While the requirements above apply for both commercial and residential rooftop solar arrays, the regulation’s inverter placement rules are more challenging for small, pitched-roof projects to satisfy. The code requires that an inverter be placed within 1 ft of the array boundary, which isn’t common practice for residential arrays. The workaround for that is using a string isolation device to separate the rapid shutdown function from the inverter. By installing a string isolation device on the roof, the inverter can be placed elsewhere, like inside the garage, while the project stays code-compliant.
“One of the big challenges that the industry saw with residential implementation of 3741 is nobody wants a big inverter on their roof, and a lot of the residential inverters aren’t necessarily rated to be installed up on your roof, on a pitched system,” Martinez said.
Motivations for being UL 3741-compliant
At a base level, UL 3741’s primary concern is protecting first responders and requires that complete solar arrays undergo a series of tests to ensure a firefighter doesn’t get electrocuted. These tests are simulating scenarios where a firefighter in full protective gear could encounter a shock hazard on the array, like kneeling or falling onto the system, or even dropping an axe through it — including panels and racking.
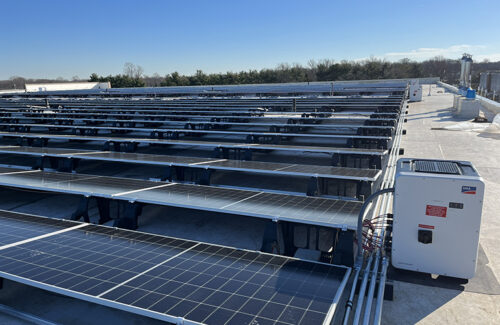
Sollega FastRack is a flat roof racking system made of non-conductive polymer, lending itself to meeting shock hazard standards in UL 3741.
“The racking is holding everything together, so in a way it does make sense,” de Papp said. “If you’re thinking about firefighter safety, the racking is central to that, and certainly inside the array field, all of the wire management is happening, typically, either through conductors that are directly attached to the racking using wire management that’s provided by the racking vendor or off-the-shelf components.”
Beyond reducing shock hazards, UL 3741 can also reduce solar project equipment costs and labor time. Not installing MLPE means saving that much per component based on how many modules are on an array. It also means installers won’t have to spend time attaching them to every module.
UL 3741 is a living safety measure and is expected to receive continual updates. For contractors considering building a UL 3741-compliant solar array, consult manufacturers to determine what inverter and racking combinations qualify.
“There’s still a lot of contentiousness around this standard,” said Yann Schwarz, VP of systems engineering and compliance at Enstall. “Obviously, there’s concern about the clarity of the certification, both from the manufacturer’s manuals and from the [Nationally Recognized Testing Laboratory]. I think in many cases that’s very much justified, because it’s not always clear, and as an industry we need to do better, because it needs to be clear what the rules are of how to build these systems and what really encompasses a thorough certification.”
I appreciate Yann’s quote “as an industry we need to do better”. An example of this can be seen in the second picture with the Sollega and SMA equipment which is an excellent example of a non-compliant system, due to lack of understanding at both the manufacturer, NRTL, AHJ, and manufacturer level. The DC array wires visible between the inverter and the array aren’t protected. If a fire fighter were to fall in that location and damage the wires or connectors they would be in contact with deadly voltage and grounded metal parts to complete the circuit. UL 3741 will need urgent revisions, NRTLs will need better training, and manufacturers will need add more protection for these systems to adequately provide a layer of safety for first responders.